Carbon prepregs, our raw materials
Often 0.3mm thick, the epoxy pre-impregnated carbon fabrics guarantee our hollow parts mechanical toughness and lightness resistance.
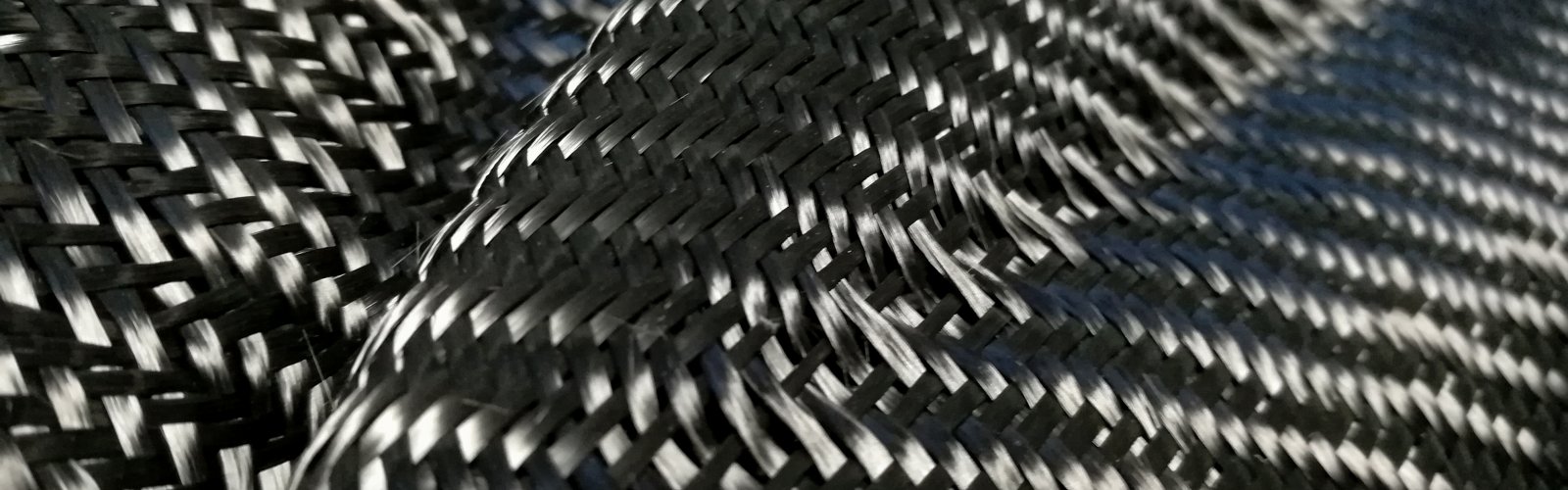
Here is a small explanation of carbon fibre, its processing and our patents...
Carbon, our raw material
It’s extremely fine fibre, with a diameter of less than 10 micrometres, is obtained after the carbonisation of a chemical precursor (polyacrylonitrile; PAN for most carbon fibres). Most of it comes from Japan, the USA, Germany and China, but the Japanese Toray also produces in France, and the American Hexcel also built a factory there.
Fibres are made of carbon atoms arranged in a crystallised pattern that are aligned in parallel to the longitudinal axis of the fibre. This makes it incredibly strong. Thousands of fibres are then winded to make the yarns, which are aligned or woven in various orientations (unidirectional, biaxials at ±45° and at 0/90°, tri and quadriaxial fabrics), then impregnated with epoxy resin. Unidirectional fabrics haven areal weight of 50g/m² to 1600g/m² and are delivered in widths from 25mm to 1600mm.
We receive these prepregs as rolls weighing between 20 to 60 kilograms and measuring 30 to 100m². We ensure the traceability of the material, as well as its storage in a minus twenty degrees centigrade freezer container. Depending on the mechanical stresses on the part which will be built, we calculate the laminate and create the layup plan, which combines various fibre orientations and thicknesses. Sometimes, parts are built as per customer supplied drawings who have directly calculated the load cases. For the most frequently used areal weight, one ply is 0.3mm thick. The layup in the moulds operation hence requires precision and rigour, so that the plies are stacked as per the engineering.
The art of lay-up and polymerisation under 7 bars of pressure
We lay up in two-half female moulds. The moulds are either machined in solid aluminium, or made in-house from a plug made of machinable resin cast, on which we infuse dry carbon fabrics with epoxy resin. The moulds need to be perfectly airtight to withstand the autoclave pressure. We also have a few construction secrets in this subject area.
The future part, in its mould, is placed in the autoclave where it will be cured up to hundred and twenty degrees and seven bars, so a very high pressure, which will heighten the mechanical properties. Like the recipes of the famous chefs, our autoclave curing processes have been optimised with patience and are very confidential.
Our innovative process for building carbon composite parts is protected by pending patents
Our process for single process hollow parts that reinforced by shear webs for a perfect spreading of the loads is protected by 2 patents. This exclusive and versatile process allows for the production of structural parts without any limitations in the shape geometry. The hollow parts are lighter and require less carbon, which is an expensive material. The one-cure build optimises the strength of the parts and allows for a marked improvement in aesthetic appearance. This also prevents the need for machining after moulding, and therefore reduces the carbon dust generated when using traditional methods.
The parts obtained demonstrate excellent mechanical properties, especially in tension and compression, and can be up to six times lighter than steel parts for the equivalent strength. Effectively, the density of a carbon epoxy composite is 1.5, compared with 7.8 for steel (hence 7.8 tonnes for 1 cubic meter). However the cost is different and it requires the rethink of all of the functions of the part, in a value analysis, or a cost orientated re-design.
Parts made by Heol Composites since 2002 have been used for a variety of applications and in very different fields (competitive sailing, automotive racing, aeronautics, industry) to the great satisfaction of our clients.
Suivez Heol Composites sur les réseaux